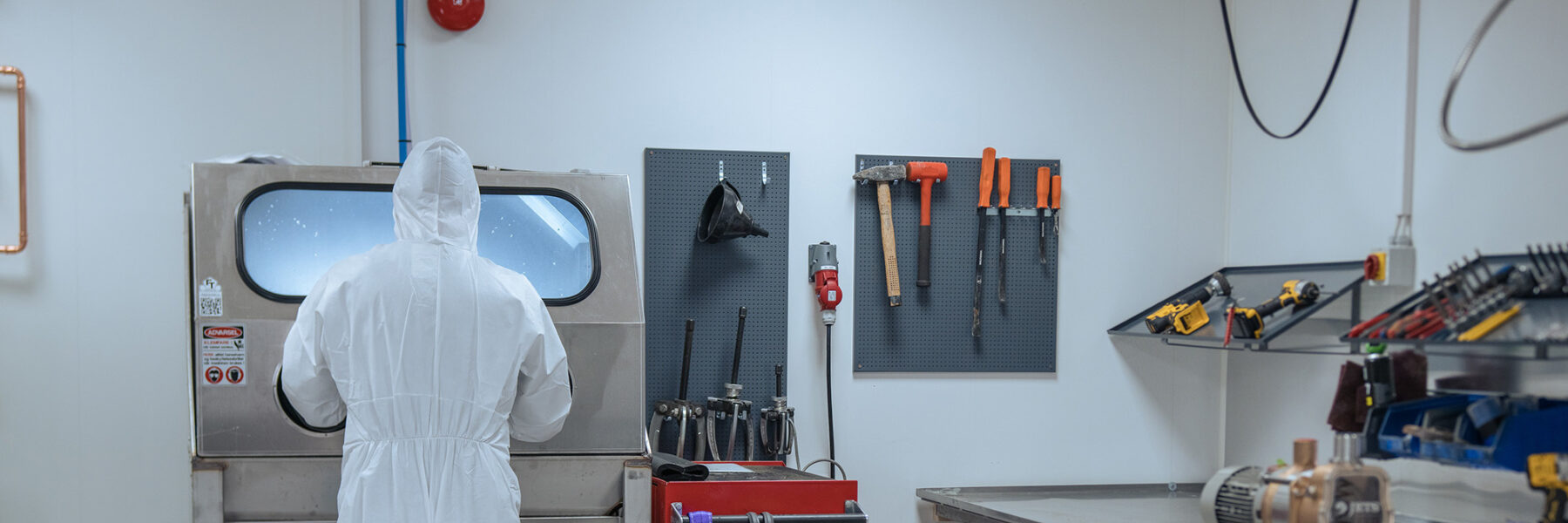
New service cells gives the Exchange Pool a boost
JETS has for many years offered pump replacement through our Exchange Pool programme, where customers send in used units and receive an overhauled pump in return. In 2024, the company took a major step forward by upgrading the scheme with a brand-new service cell at its headquarters in Hareid.
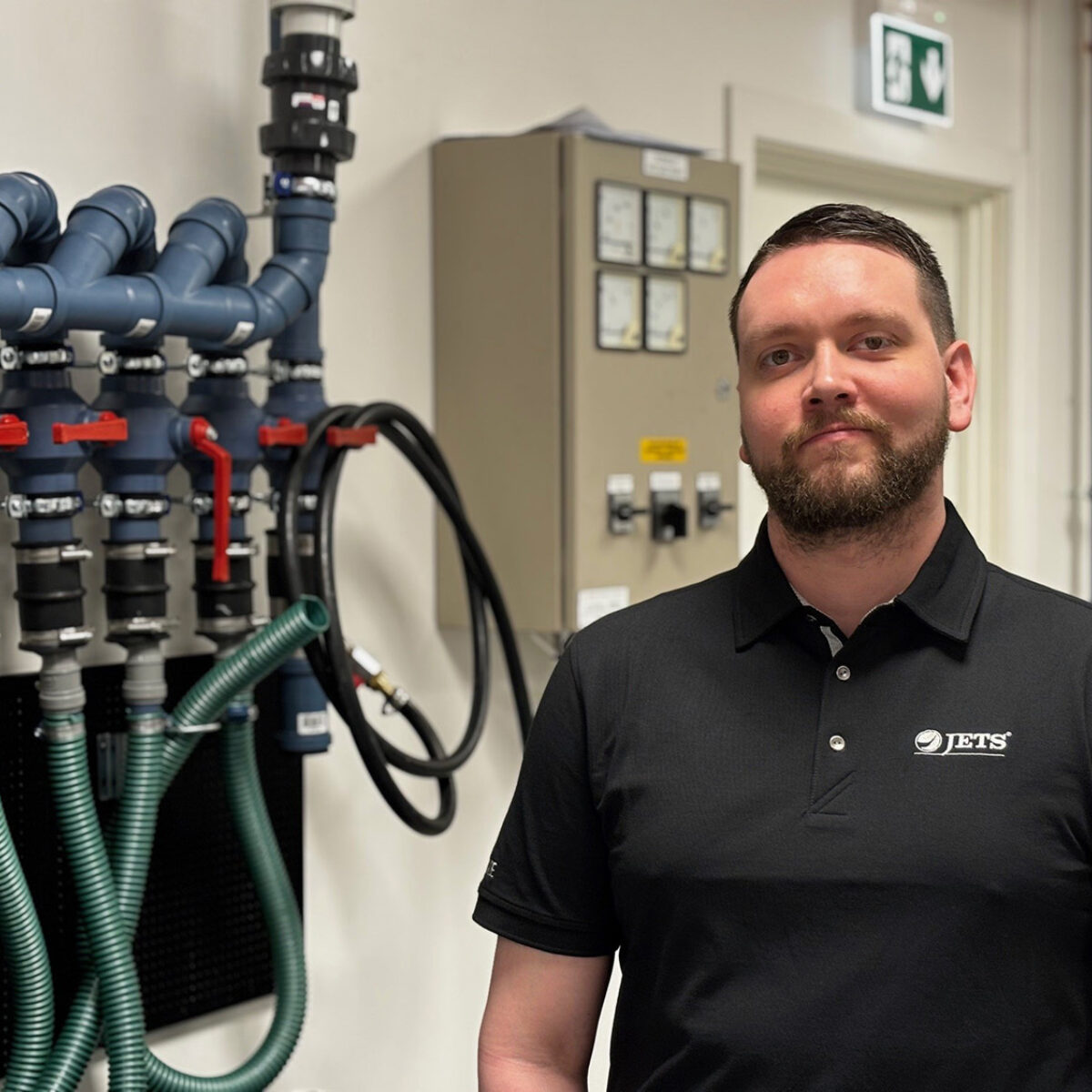
The aim was to make the Exchange Pool both more streamlined and transparent. Clear process maps were introduced, along with improvements across all departments. This has strengthened both the capacity and the quality of customer service.
– When we overhaul a pump, we give it a new life. And with our new facilities, we do it better, safer and more efficiently than ever before, says Kristian Øvreberg Hellebust, Service Manager at JETS.
Each pump has its own unique serial number, enabling full traceability throughout the entire process – from the point it is received, through overhaul and testing, to final delivery. Original pumps, new units and overhauled ones are all clearly identified and separated.
New facilities for precise and secure overhauls
At first glance, the new service area may look like an ordinary workshop, but inside, everything is carefully planned. The space is divided into dedicated zones that ensure hygiene, safety and precision at every stage of the process.
– We have separate clean and dirty zones, proper protective equipment, and clear routines. Nothing happens by chance here, says Hellebust.
Incoming pumps are disassembled, cleaned, water-polished and tested before being returned to the customer. The result is a pump that is as good as new – with a new serial number and a completely renewed lifecycle.
Ready when you need it
– A replacement pump is typically required when an overhaul is carried out, especially if the condition of the existing pump is uncertain. It might be wear and tear, a performance check, or an unknown fault that needs closer assessment. In some cases, time pressure means a replacement pump is just as fast as ordering and fitting spare parts, explains Raymond Hovlid, Sales Manager Aftermarket.
For many customers, this means they can keep operations running smoothly, without unexpected downtime or the need to invest in completely new equipment.
– It’s a win-win situation. Customers get a reliable solution at a fair price, and we keep products in circulation. It’s cost-effective and environmentally responsible, says Hovlid.
Efficient and sustainable operation – with no compromise
For companies looking to reduce downtime and operating costs, using an overhauled pump is a strategically smart choice. Each unit is delivered fully tested and ready to use, offering the same performance and lifespan as a new one, but at a lower cost. The customer sends in their used pump and receives an upgraded one in return, in a system that works much like a deposit scheme.
The environmental benefits are substantial: less waste, reduced resource consumption and full traceability throughout the process. With this solution, customers gain predictability and flexibility, without compromising on quality.
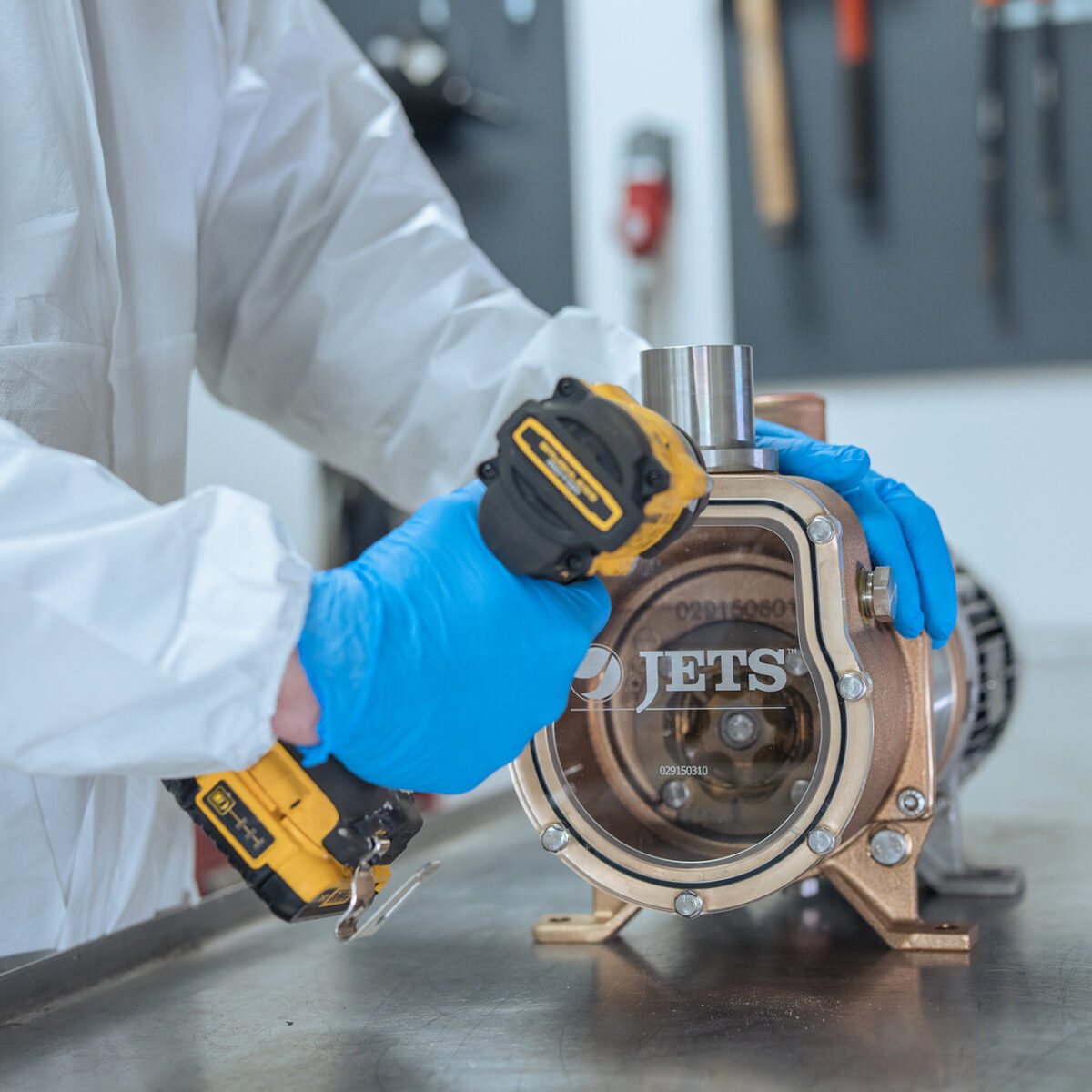
Solutions that last
At JETS, development is about more than delivering good results today, it’s about ensuring reliable, cost-effective and sustainable solutions over time. The Exchange Pool programme is a clear example of this. By offering overhauled pumps as an alternative to new ones, customers get quicker deliveries, lower resource usage and full traceability – without sacrificing quality or durability.
– We know that replacing a pump quickly can be critical for our customers. That’s why we provide fully prepared units, ready to use, with a 12-month warranty. Once the old unit is returned, the deposit is credited. Simple and effective, says Hovlid.
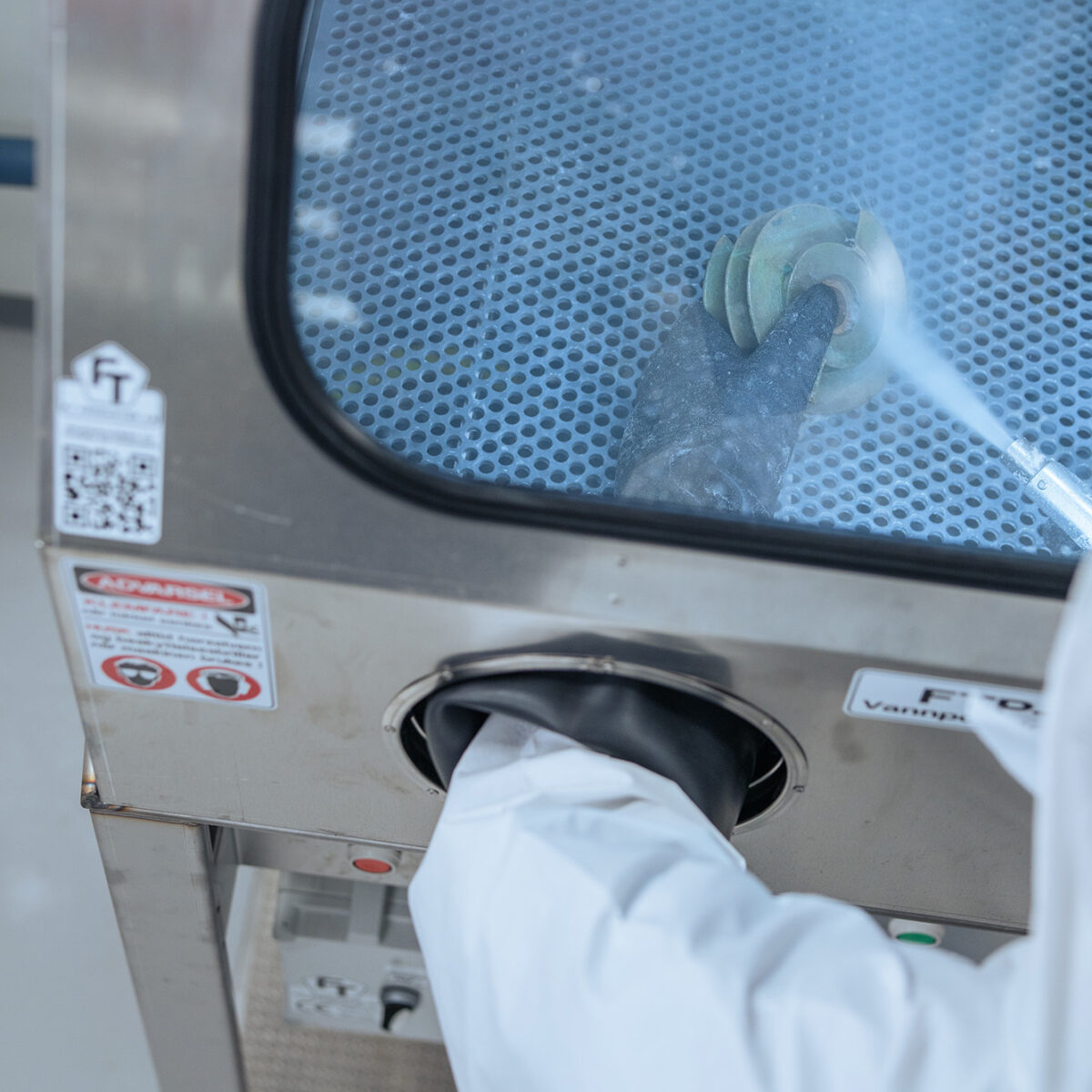
Close contact strengthens service and relationships
– We run a support centre that works closely with our customers, and much of our insight comes from hands-on field experience. This allows us to better understand their needs – and recommend smart solutions, like the Exchange Pool, says Hellebust.
– There’s definitely room for more customers to benefit from the programme. So far, we’ve offered it where we’ve seen it to be a good fit for customers we’re already in contact with. But if others are interested in learning more or considering joining, they’re very welcome to reach out, he adds.
Circular thinking in practice
When we talk about sustainability and circularity, the focus often shifts to new innovations. But frequently, the solution lies in what we already have and how we take care of it.
– The smartest solutions aren’t always new. Often, with durable products like the Vacuumarator®, it’s about making the most of what you already have. That requires a solid maintenance plan and a commitment to taking care of the system over time. That’s exactly what the Exchange Pool puts into practice, says Hellebust.
This is about more than just keeping pumps running. It’s about building trust. About being a partner who sees opportunities, thinks long-term, and delivers what they promise.
Good solutions shouldn’t only work today. They should last – and ideally improve over time. With the Exchange Pool programme and a new service cell in place, JETS has taken an important step towards a more responsible and flexible future – both for the company and for its customers.